In 3D FDM là gì. Cách hoạt động và các đặc điểm của công nghệ in 3D FDM
1. In 3D FDM
Về cơ bản, in 3D FDM là mô hình hóa lắng đọng hợp nhất, hay còn được gọi là chế tạo dây tóc hợp nhất (FFF). Là một quy trình sản xuất phụ gia bằng cách đùn vật liệu. Trong FDM, một đối tượng được xây dựng bằng cách lắng đọng có chọn lọc vật liệu nóng chảy theo một đường dẫn định trước, từng lớp một được xếp chồng lên nhau. Vật liệu được sử dụng là polyme nhiệt dẻo, có dạng sợi.
FDM là công nghệ in 3D được sử dụng rộng rãi nhất hiện nay. Bởi tính dễ sử dụng và là sự lựa chọn ưu tiên của các nhà sản xuất để tạo mẫu nhanh chóng, thêm vào đấy là chi phí thấp (cả về nguyên vật liệu và máy móc).
2. Máy in 3D FDM hoạt động như thế nào?
Quá trình chế tạo mẫu in FDM hoạt động bằng cách, đầu tiên cho một sợi nhựa nhiệt dẻo vào máy in, hi vòi phun đã đạt đến nhiệt độ mong muốn (190 – 230oC tùy vào từng vật liệu), sợi nhựa sẽ được đưa vào đầu đùn và vòi phun, nơi vật liệu nóng chảy.
Đầu đùn được gắn vào một hệ thống ba trục di chuyển theo các hướng x-, y- và z-. Vật liệu nóng chảy được đùn thành từng sợi mỏng và lắng đọng thành từng lớp ở những vị trí xác định trước, nơi nhựa nguội đi và đông đặc lại. Quạt có thể được gắn vào đầu đùn để tăng tốc độ làm mát.
Để lấp đầy một khu vực, cần có nhiều đường chuyền. Khi một lớp hoàn thành, nền tảng xây dựng sẽ di chuyển xuống (hoặc trong một số thiết lập máy, đầu đùn di chuyển lên) và một lớp mới lại được đặt vào. Quá trình này được lặp lại cho đến khi phần hoàn tất.
2.1 Thông số máy in FDM
Hầu hết các hệ thống FDM cho phép điều chỉnh một số tham số quy trình. Chúng bao gồm nhiệt độ của cả vòi phun và nền tảng, tốc độ xây dựng, chiều cao lớp và tốc độ quạt làm mát. Thường trước khi in mỗi mẫu, các kỹ thuật viên phải nghiên cứu và cho ra thông số tối ưu nhất để sản phẩm khi in ra được tốt nhất, không bị hư hỏng nặng (các thông số không thay đổi quá nhiều).
Tuy nhiên, kích thước bản dựng và chiều cao lớp cũng khá quan trọng
Kích thước vùng của máy in 3D để bàn thường là 200 x 200 x 200mm, trong khi máy công nghiệp có thể lớn tới 1.000 x 1.000 x 1.000mm. Tuy nhiên, đối với những mẫu in lớn quá khổ, kỹ thuật viên cần phải tiến hành cắt file in để chia tách thành các bộ phận nhỏ hơn. Và sau đó lắp ráp lại, ngoài ra, một số mẫu nên cắt file để giảm phần support và để bề mặt đẹp hơn.
Chiều cao lớp điển hình được sử dụng trong FDM thay đổi từ 50 đến 400 micrômét và có thể được xác định khi đặt hàng. Một lớp có chiều cao ngắn hơn tạo ra các bộ phận mượt mà hơn và chụp các hình dạng cong chính xác hơn, trong khi chiều cao lớn hơn tạo ra các bộ phận nhanh hơn và tiết kiệm chi phí hơn.
2.2 Đặc điểm của in 3D FDM là gì?
1. Cong vênh
Cong vênh là một trong những lỗi phổ biến nhất trong FDM. Khi vật liệu ép đùn nguội đi trong quá trình đông đặc, kích thước của nó giảm. Vì các phần khác nhau của bản in nguội ở các tốc độ khác nhau, nên kích thước của chúng cũng thay đổi ở các tốc độ khác nhau. Làm mát khác biệt gây ra sự tích tụ của ứng suất bên trong kéo lớp bên dưới lên trên, làm cho nó bị cong vênh.
Có thể ngăn ngừa sự cong vênh thông qua giám sát nhiệt độ chặt chẽ hơn của hệ thống FDM (như dựng thêm bệ và buồng kín để đảm bảo nhiệt độ) giúp tăng độ bám dính giữa mẫu và bàn in, hay ngay từ lúc bắt đầu in chúng ta nên bôi keo để tăng độ bám dính và quan sát cho đến khi mẫu in ổn định (khoảng đến lớp thứ 10)
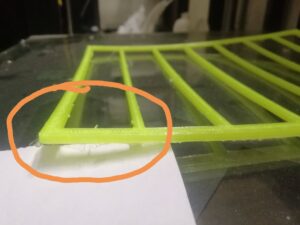
Thêm một số chi thiết kế cũng có thể làm giảm khả năng cong vênh:
- Các khu vực phẳng lớn (chẳng hạn như những đặc điểm của hình hộp chữ nhật) dễ bị cong vênh hơn và nên tránh khi có thể.
- Các đặc điểm nhô ra mỏng cũng dễ bị cong vênh. Có thể tránh cong vênh bằng cách thêm vùng in (tránh phần ảnh hưởng tới mẫu in) ở cạnh của điểm mỏng đó, để tăng diện tích tiếp xúc với bàn in.
- Các góc sắc nhọn thường bị cong vênh hơn so với các hình tròn, vì vậy việc thêm các miếng phi lê vào thiết kế là một phương pháp hay.
- Các vật liệu khác nhau dễ bị cong vênh hơn. ABS thường nhạy cảm với cong vênh hơn PLA hoặc PETG.
2. Độ bám dính của lớp
Sự kết dính an toàn giữa các lớp lắng đọng là rất quan trọng đối với một bộ phận FDM. Khi nhựa nhiệt dẻo nóng chảy được đùn qua vòi phun, nó sẽ được ép vào lớp đã in trước đó. Nhiệt độ và áp suất cao làm cho lớp này nóng chảy lại và tạo điều kiện cho lớp mới liên kết với phần đã in trước đó.
Độ bền liên kết giữa các lớp khác nhau luôn thấp hơn độ bền cơ bản của vật liệu. Điều này có nghĩa là các bộ phận FDM vốn có tính dị hướng: độ bền của chúng theo trục z luôn nhỏ hơn độ bền của chúng trong mặt phẳng XY. Vì lý do này, điều quan trọng là phải xem xét khi thiết kế các bộ phận cho FDM, và cách cài đặt các thông số trước khi in.
Vì vật liệu nóng chảy được ép vào lớp đã in trước đó, hình dạng của nó bị biến dạng thành hình bầu dục. Đây là nguyên nhân mà các bộ phận FDM luôn có bề mặt gợn sóng, bất kể là cài đặt chiều cao lớp nào, tùy vào chiều cao lớp bao nhiêu để quyết định bề mặt vật in, có thể cần được xử lý hậu kỳ sau khi in.
3. Hỗ trợ cấu trúc hạ tầng (support)
Vì nhựa nhiệt dẻo nóng chảy không thể lắng đọng trong không khí loãng nên một số dạng hình học cần có suport
Support có thể khó tháo gỡ, vì vậy việc thiết kế các bộ phận tránh làm diện tích tiếp xúc phần support với mẫu in quá lớn.
Hỗ trợ thường được in bằng vật liệu giống như bộ phận. Vật liệu hỗ trợ hòa tan trong chất lỏng cũng tồn tại, nhưng chúng được sử dụng chủ yếu trong máy in 3D FDM công nghiệp hoặc máy tính để bàn cao cấp. Vì là có phần support nên sẽ tăng khối lượng mẫu in từ đó tăng chi phí tổng thể của một bản in.
4. Infill và độ dày thành
Để giảm thời gian in và tiết kiệm vật liệu, các bộ phận FDM thường không được in rắn. Thay vào đó, lớp vỏ bên ngoài được in dày khoảng 1-3mm, và bên trong được lấp đầy bằng các đường infill với mật độ thấp hơn
Độ dày của lớp đệm và lớp vỏ ảnh hưởng rất nhiều đến độ bền của bộ phận. Đối với máy in FDM để bàn, cài đặt mặc định là mật độ nhựa in 20% và độ dày vỏ 1mm, điều này sẽ giúp bản in tăng độ cứng, tiết kiệm nhựa in và thời gian hoàn thành mẫu in nhanh chóng.
Các đặc điểm chính của FDM được tóm tắt trong bảng này:
Vật liệu | Nhựa nhiệt dẻo (PLA, ABS, PETG, PC, PEI, v.v.) |
Độ chính xác về chiều | ± 0,5% (giới hạn dưới ± 0,5 mm) – máy tính để bàn ± 0,15% (giới hạn dưới ± 0,2 mm) – công nghiệp |
Kích thước bản dựng điển hình | 200 x 200 x 200 mm – máy tính để bàn 900 x 600 x 900 mm – công nghiệp |
Độ dày lớp chung | 50 đến 400 micrômét |
Hỗ trợ (support) | Các mẫu lớn và phức tạp cần phải có phần hỗ trợ, tuy nhiên không phải mẫu in nào cũng cần support. |
5. Vật liệu FDM phổ biến
Một trong những điểm mạnh chính của FDM là nhiều loại vật liệu có sẵn để sử dụng. Bao gồm nhựa nhiệt dẻo (như PLA và ABS ), vật liệu kỹ thuật (như PA, TPU và PETG ) và nhựa nhiệt dẻo hiệu suất cao (như PEEK và PEI).
Vật liệu được sử dụng ảnh hưởng đến các đặc tính cơ học và độ chính xác của bộ phận in cũng như giá thành của nó. Các vật liệu FDM phổ biến nhất được tóm tắt trong bảng dưới đây. Để biết thêm chi tiết, hãy xem bài đánh giá này về sự khác biệt chính giữa PLA và ABS — hai vật liệu FDM phổ biến nhất — và so sánh sâu rộng về tất cả các vật liệu FDM phổ biến, bên dưới.
Vật chất | Đặc trưng |
ABS | + Chịu lực tốt + Chịu nhiệt độ tốt – Dễ bị cong vênh |
PLA | + Chất lượng hình ảnh tuyệt vời + Dễ dàng in ấn – Độ bền va đập thấp |
Nylon (PA) | + Độ bền cao + Chống mài mòn và hóa chất tuyệt vời – Độ ẩm thấp |
PETG | + An toàn thực phẩm * + Độ bền tốt + Dễ in bằng |
TPU | + Rất linh hoạt + Có tính dẻo – Khó in chính xác |
PEI | + Chịu được trọng lượngtốt + Chống cháy và chống hóa chất tốt – Giá thành cao |
6. Xử lý hậu kỳ
Các bộ phận in 3D FDM có thể được hoàn thiện với tiêu chuẩn rất cao bằng cách sử dụng các phương pháp xử lý sau khác nhau, chẳng hạn như chà nhám và đánh bóng, sơn lót và sơn, hàn nguội, làm mịn hơi, sơn epoxy và mạ kim loại. Có nhiều tùy chọn xử lý hậu kỳ cho các bộ phận FDM .
3. Ưu điểm của in 3D FDM là gì?
- Ưu điểm lớn nhất của FDM là chi phí rẻ (cả về nguyên liệu và máy móc) để sản xuất các bộ phận và nguyên mẫu nhựa nhiệt dẻo tùy chỉnh.
- Thời gian thực hiện ngắn (thường là vài ngày) do tính phổ biến của công nghệ.
- Nhiều loại vật liệu có sẵn, phù hợp cho cả việc tạo mẫu và một số ứng dụng chức năng.
4. Nhược điểm của in 3D FDM là gì?
- FDM có độ phân giải thấp nhất so với các công nghệ in 3D khác nên không phù hợp với các bộ phận có chi tiết quá nhỏ.
- Các bộ phận có thể có các đường lớp có thể nhìn thấy được, vì vậy cần phải xử lý hậu kỳ để có lớp hoàn thiện mịn.
- Cơ chế kết dính lớp làm cho các bộ phận vốn có tính dị hướng.
5. Các phương pháp hay nhất về FDM
- FDM có thể sản xuất nguyên mẫu và các bộ phận chức năng một cách nhanh chóng và tiết kiệm chi phí.
- Có nhiều loại vật liệu có sẵn cho FDM.
- Kích thước xây dựng điển hình của máy in 3D FDM để bàn là 200 x 200 x 200mm. Máy công nghiệp có kích thước xây dựng lớn hơn.
- Để tránh cong vênh, hãy tránh những khu vực phẳng lớn và thêm phi lê vào những góc sắc nhọn.
- FDM vốn có tính dị hướng, vì vậy nó không phù hợp với các thành phần quan trọng về mặt cơ học.
Bạn muốn tìm hiểu thêm về in 3D? Đọc hướng dẫn đầy đủ của chúng tôi: In 3D là gì?
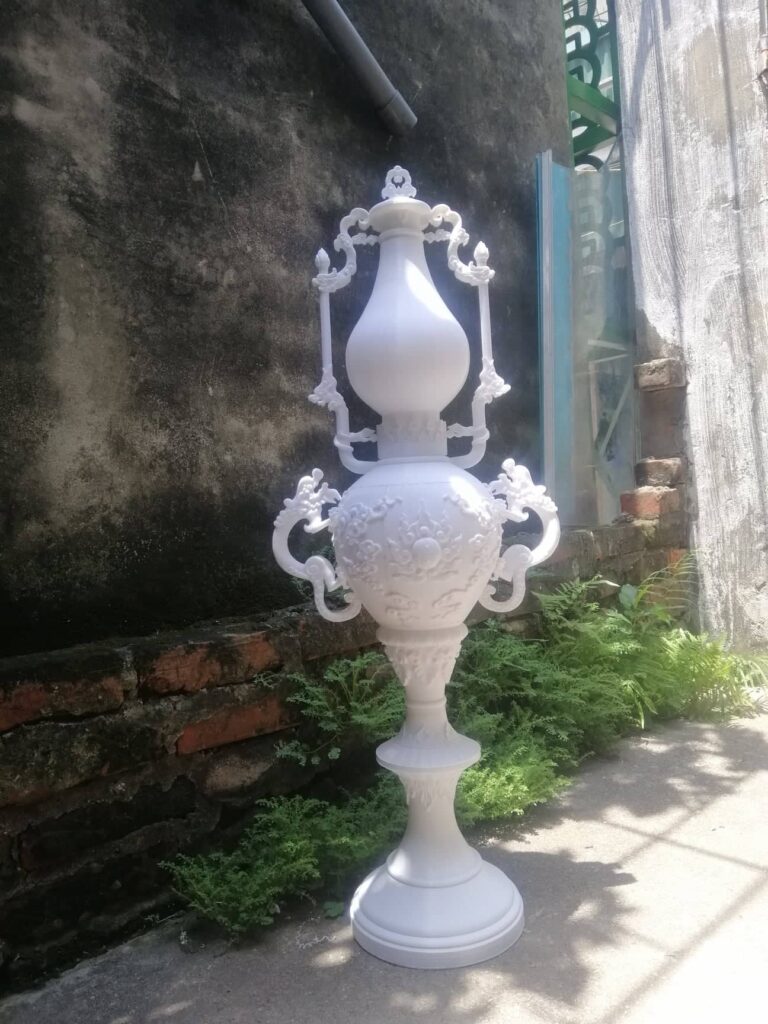
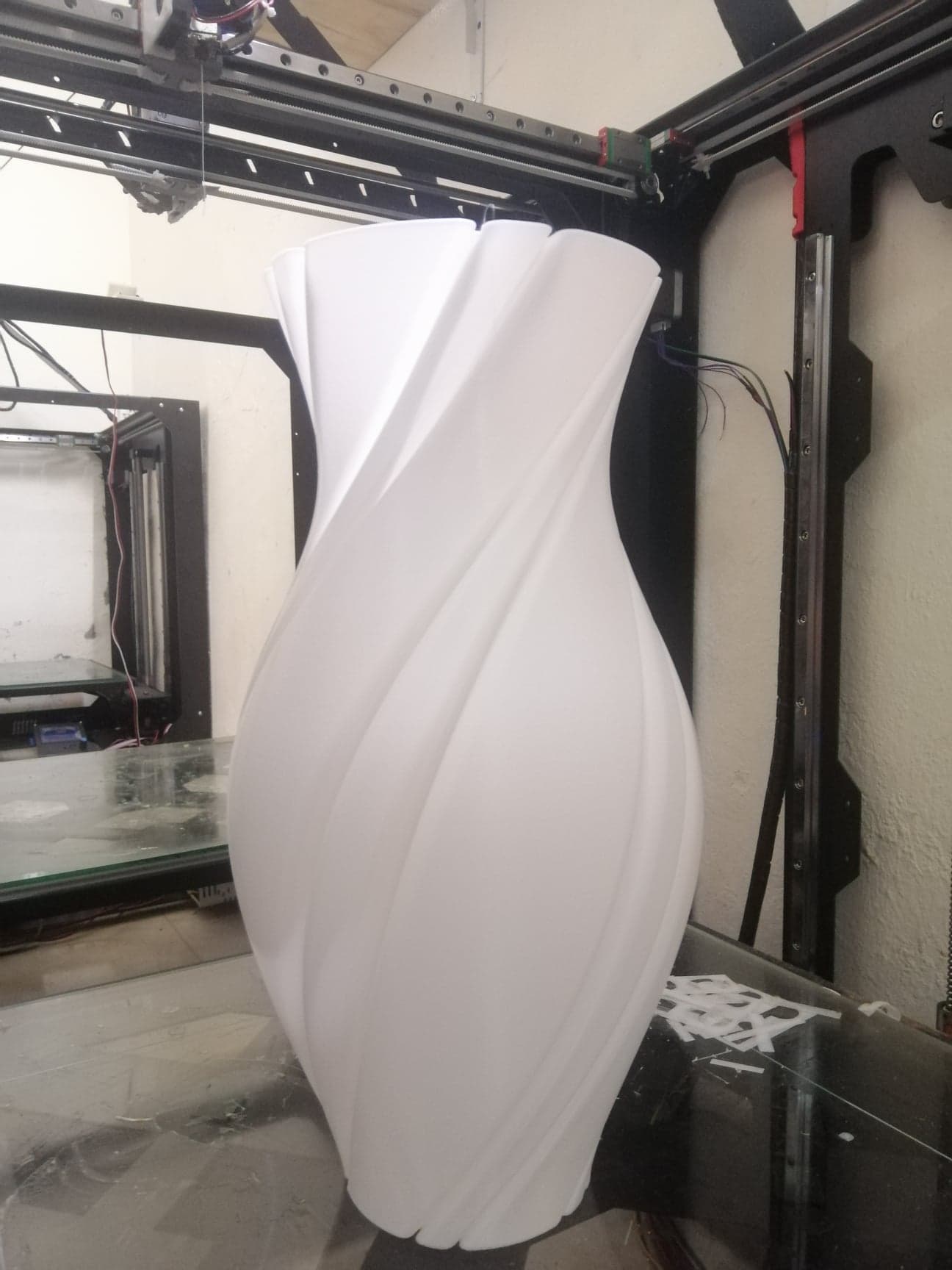
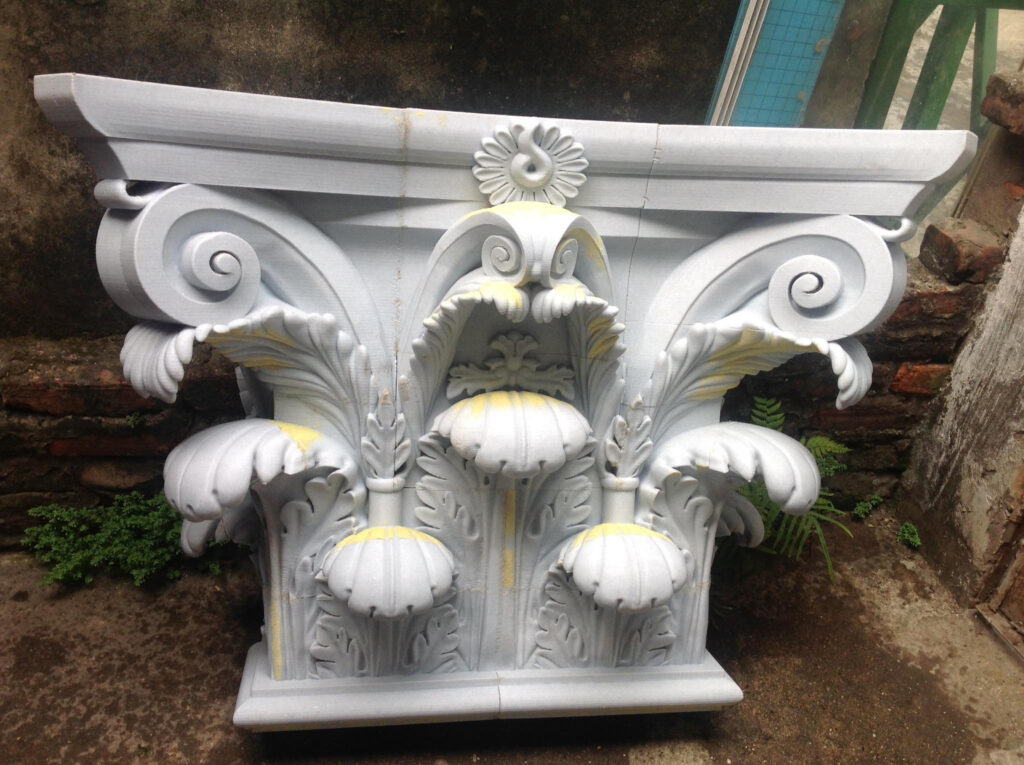